Last Updated on October 23, 2023 by softtech
Abstract
Mega-scale infrastructure projects provide a unique opportunity to turbo charge digital transformation in the construction industry. Such projects give a unique opportunity to address several sector specific challenges such as interoperability, resistance to change, industry fragmentation, skills gap, complex supply chains, and a lack of technology integration. Technologies like digital twin, building information modeling (BIM), and cloud-based information management systems will play a crucial role in this transformation. By embracing these solutions, the construction industry can improve efficiency, safety, and sustainability in mega projects, driving overall progress and development.
Key takeaways
- Construction Industry Challenges:
- Interoperability
- Resistance to change
- Industry fragmentation and
- skills gap
- Solutions:
- Digital Twin
- BIM and
- Cloud base Information Management System
- Technology adoption via Mega infrastructure projects
Introduction
Large infrastructure projects are mega-scale and complex undertakings generally with an aim to create sustainable infrastructure that improves connectivity, productivity, and competitiveness of a region or a country. These mega projects or infrastructure developments entail construction or expansion of transportation networks, energy systems, industrial zones, urban centers, commercial centers, residential communities, and other facilities that support the social and economic development of society. In the current times, there are multiple examples of such mega undertakings such as NEOM, the Trans-European Transport Network (TEN-T) and the Delhi-Mumbai Industrial Corridor (DMIC) among several others.
Such projects present the opportunity to further the existing state-of-practice because of their scale and impact, especially in the infrastructure sector where adoption of technology is relatively low and limited. However, we observe greater interest in the construction industry towards understanding and adopting concepts of industrialized construction to help capture a much greater breadth of benefits due to technology adoption.
The three general areas where we, as technology providers, are seeing good uptick and interest in the construction industry are
- Integrated planning and project management systems
- Sustainability embedded at every stage of the asset lifecycle
- Enhancing visibility to and experience of end-users of the asset
There are multiple solutions that address part of the above specified areas. The solutions are typically enabled by underlying technologies such as Digital Twin, BIM, and cloud-based information management systems. However, in our experience, the technology adoption has largely been in silos and limited to confined use cases.
Challenges:
Given below are some of the specific challenges which are inhibiting the digital transformation of the construction industry.
-
- Lack of interoperability and standardization among different systems and platforms:Given the wide spread of the stakeholders, it becomes a challenge to integrate and analyze data across the project lifecycle which leads to inefficiencies, errors, and delays.
- The resistance to change:
The construction industry is traditionally conservative and risk-averse, and many stakeholders are reluctant to adopt new technologies and methods that may disrupt their established practices and routines. This hinders the diffusion and adoption of digital innovations and requires a cultural shift and a change management strategy.
- The fragmentation of the industry: The construction sector is composed of many different actors, such as owners, contractors, subcontractors, suppliers, designers, and consultants, who often have different interests, goals, and standards. This makes it difficult to coordinate and integrate the various digital tools and processes across the project lifecycle.
- The lack of skills and competencies: The digital transformation requires new skills and competencies for the construction workforce, such as data literacy, digital collaboration, and process standardization. However, there is a shortage of qualified and trained workers who can use and benefit from digital technologies and solutions. This creates a gap between the demand and supply of digital skills and competencies in the industry.
- Complex supply chain:The construction industry involves a complex supply chain, with many different stakeholders involved in a project. This can make it difficult to implement technological solutions that require coordination between different parties.
- Afterthought approach towards technology adoption:The industry has not taken up the approach of intuitively thinking of technology integration at all levels of the project delivery at the project conceptualizing level. Technology solutions are generally inserted as an afterthought. This creates issues for technology adoption at scale due to lack of standardization and interoperability.
However, there is a growing recognition of the potential benefits of technology adoption, and the construction community is taking efforts to overcome these barriers and promote wider adoption in the industry.
Digital twin, building information modeling (BIM), and cloud-based information management systems offer transformative solutions to the challenges hindering the construction industry’s digital transformation. Overcoming obstacles like interoperability, resistance to change, industry fragmentation, and skills gap, their adoption is crucial for creating sustainable infrastructure that enhances connectivity, productivity, and competitiveness. Mega infrastructure projects like NEOM, TEN-T, and DMIC can drive technology adoption, showcasing benefits, fostering collaboration, and establishing industry standards. Lessons learned from these projects can accelerate their broader integration in construction.
Solutions:
Mega infrastructure projects present the opportunity to address the challenges listed above. Given the scale, timelines, and involvement of majority of the stakeholders these mega projects present a unique opportunity to take huge strides in digital transformation of the construction industry. Let us dive into three specific underlying technologies that will form the core of digital solutions of the future in the construction industry
- Digital Twin:
A digital twin is a virtual representation of a physical building or infrastructure project that captures its geometry and other aspects. It revolutionizes construction projects by enhancing design, construction, and management, leading to efficiency, cost savings, and better decision-making. Let us look at the applications from three different contexts
a. Project/City-level
Digital twins enable architects and engineers to create and visualize complex building designs in a virtual environment. Once the base model is generated, they can very quickly explore different design options, test various materials and configurations, and analyze the impact on aesthetics, functionality, and constructability. By simulating the interaction of these systems within the digital twin, potential clashes can be detected and resolved before construction begins, reducing costly rework and delays.
b. Safety
Digital twins support construction planning by simulating and optimizing construction sequences, logistics, and resource allocation. With digital twin simulating safety scenarios and evaluating potential risks during construction is possible. They can analyze safety hazards, assess the effectiveness of safety measures, and train workers on safety protocols. This helps improve worker safety and reduces the occurrence of accidents on the construction site. Virtual training can be facilitated by Digital twins for construction workers, allowing them to familiarize themselves with complex construction processes and equipment before starting on-site work. This can be done without putting the employee in harm’s way and can be repeated/tweaked quite easily.
c. Sustainability
Digital twins can be used to simulate and evaluate different renovation strategies for existing buildings by assessing the impact of changes on structural integrity, energy efficiency, and overall performance, enabling informed decision-making during retrofitting or renovation projects. Digital Twins can integrate real-time data from sensors, IoT devices, and equipment to monitor how an asset is performing. Gaining this understanding will lead to optimizing the asset performance with a goal of efficiency and sustainability.
The utilization of digital twins in the construction sector is constantly progressing and a variety of innovative technologies are being incorporated to enhance their effectiveness. These include building information modelling (BIM), internet of things (IoT), augmented reality (AR), virtual reality, artificial intelligence (AI), machine learning (ML), cloud computing, blockchain technology, light detection and ranging (LiDar) scanning technology, robotics and automation, and more.
For example, enabling real-time visibility or visualization- Leverage metaverse, augmented reality (AR), virtual reality (VR), and mixed reality (MR) coupled with digital twin. These technologies can be used to create immersive experiences for stakeholders. Stakeholders can use metaverse to visualize an apartment in a real-world environment or to see how a construction project will look once completed.
- Building Information Modeling (BIM):
BIM is a digital process that enables collaboration and coordination among different stakeholders in the construction industry. BIM allows for the creation and management of 3D models that contain information about the design, construction, and operation of a building. BIM could act as the base for creation of the digital twin for the asset. Listed below are some of the more novel use-cases
a. Project or City-Level
Design analysis in value engineering: Estimation of material BOQ, optimal usage of space, energy efficient orientation, daylight analysis, system sizes, capacities, consumption prediction, clash detection and many more application including the possibility of safe evacuation during emergencies. This early-stage analysis can save the project significant capital whilst estimating the performance under various categories including estimation of embodied carbon and operational carbon.
Retrofit analysis syncs the building with the possibility of upgrading its operational efficiency with the advent of new technologies. The as-built BIM model now can be evaluated with advanced technologies (e.g.: the cost-benefit analysis of replacing a 5-year-old chiller with a state-of-art radiant cooling mechanism). The outputs would include cost vs. payback vs. savings. The updated BIM model will include the retrofits as and when they are incorporated along with KPIs such as updated operational carbon that captures the retrofit impacts and any new energy mix.
b. Safety
Digital twins at a city level include commute and service details. While service lines include but are not limited to electricity, water, drain, communication lines, commute roadway information such as road width, service lanes, pedestrian access, and cycling lanes. The digital twin map overlayed with live data (traffic cameras and road service interruptions) will help plan emergency movements and disaster management planning such as ambulance access, catastrophe management, calamity evacuation.
c. Sustainability
BIM-BMS integration: The ability of a BIM model to be dissected to the most basic elements makes it a perfect fit for dashboarding at a building, zone, floor, room and even to wall levels. With dynamic UIs reporting live data, a 3D digital twin dashboard has the potential to be the gamechanger at multi levels. BIM-BMS combined presents the opportunity to present thermal comfort data at a room level (AQI, CO2, temperature, humidity) followed by display of live building consumption of energy, water, per capita indices, at building to comparing best performing buildings at a portfolio, community, or city level.
Carbon Footprint and Net Zero: A live digital twin also serves as a repository of the building’s vitals (energy consumption, water consumption, HVAC loading % etc.) and this can be accessed as streams of data on demand. The data can provide insights such as building’s peak hours, renewable energy shortfall towards achieving a net zero status, estimation of rooftop and façade specific (BIPV) energy generation potential and long-term decarbonization strategies via retrofit and retro-commissioning analysis.
Green building certification requires conformance to bylaws and standards. A digital twin-based model can evaluate the energy, daylighting, water, material, and site-specific credits that are governed by both bylaw and green building standards.
- Cloud-based information management systems:
The ability to store, access, analyze, and share data in near real-time presents huge benefits to the construction industry. In addition to this capability, the cloud-based information management systems offer scalability, security, and cost-effectiveness. Such a system can help realize huge benefits for the construction industry.
a. Project/city-level
The use-cases can include aspects such as large-scale planning, automated permitting, integrated costing, near real-time optimizing, and efficient operating
Automated Permitting – This concept will enable scaling up developmental/building code rule deployment, increasing pace and uniformity of rule implementation, and collecting high-quality data that will enable creation of city-wide decision-making frameworks. For example, we have helped clients such as the municipal corporation of major cities in India to significantly improve their World Bank’s ease of doing business ranking by developing and deploying a single-window automated permitting system. The system has helped the government to collect high-quality data collection, uniform implementation of development control rules and public infrastructure assessments.
b. Safety
Cloud-based information management systems can streamline regulatory compliance processes. They can provide features such as automated reporting, document control, and audit trails, simplifying the documentation and record-keeping required to meet safety standards. This reduces administrative burdens, enhances transparency, and facilitates smoother audits.
c. Sustainability
Built environment, one of the significant contributors to the greenhouse gas emissions, presents a great opportunity to understand, optimize and operate the assets while minimizing their carbon footprint. A key enabler for this to happen at scale is a cloud-based system that helps collect, analyze, and visualize how the built asset is ‘living’. The data produced from various sources in the asset does not need to stay local and can be streamed, aggregated, and analyzed by a cloud-based information management system which then can be used to create intelligence via predictive and prescriptive analytics. Such a system will lead to a reduction in operating costs while reducing carbon emissions.
A Paradigm Shift in the Construction Industry
Digital twin, building information modeling (BIM), and cloud-based information management systems have the potential to address the specific challenges inhibiting the digital transformation of the construction industry when deployed on large-scale projects. These technologies can bring about significant improvements in efficiency, collaboration, sustainability, and decision-making throughout the project lifecycle.
Although adoption of these technologies in the construction sector has many advantages, their application brings numerous obstacles. To conquer these challenges, cooperation among all involved parties, such as building organizations, tech providers, regulators, and decision-makers is essential. Additionally, comprehensive preparation, strong project control, and consistent surveillance and review are necessary to ensure the successful use of digital twins in the construction industry.
Digital twin technology enhances design, safety, and sustainability through virtual simulations. BIM enables collaboration, design analysis, retrofit assessments, and safety planning. Cloud-based systems provide scalable and cost-effective data storage, real-time access, and analytics for improved project outcomes. These technologies foster integration, collaboration, and knowledge sharing among stakeholders, driving connectivity, productivity, and competitiveness while overcoming resistance to change. Their widespread adoption can lead to sustainable infrastructure development and benefit society.
Giga projects like NEOM, the Trans-European Transport Network (TEN-T) and the Delhi-Mumbai Industrial Corridor (DMIC) and several others, which are large-scale, transformative developments, can encourage the use of the solutions such as digital twin in the construction industry in several ways, including demonstrating proof of concept, technology adoption and investment, collaboration and stakeholder engagement, innovation, research and development, knowledge sharing and industry standards, legacy and long-term benefits.
The use of digital twins, BIM and cloud-based information management systems in the construction industry could be driven by giga projects. They provide a platform for showcasing the benefits, encouraging technology adoption, fostering collaboration, advancing innovation, and establishing industry standards. The lessons learned from these projects can catalyze the broader adoption and integration of digital twins across a wide range of construction projects.
About the Author
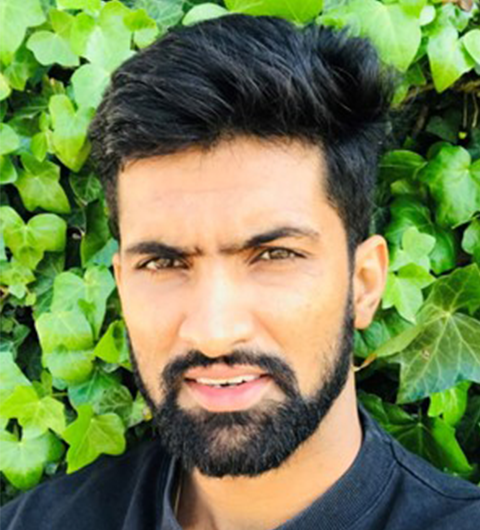
Head – Technical, Sustainability Solutions, SoftTech
Girish is a seasoned sustainability professional and specializes in the field of energy analytics including – 3D digital twin tech, city mapping for climate change, energy simulation, energy efficiency strategy formulation, ventilation designs, automation, and retrofits. With over a decade and a half’s experience, he has led award-winning green projects across sectors such as FDIs, retail chains, healthcare, hospitality, governments, and institutions working with new and operational manufacturing industries.
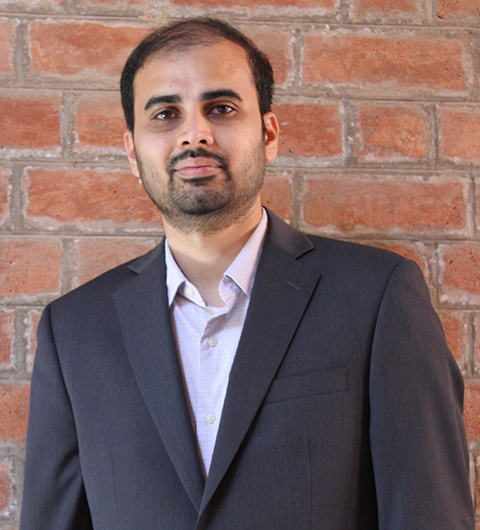
Vice President, Product Strategy & Pre-Sales, SoftTech
Kashyap has over 14+ years of international experience in civil infrastructure and the built environment industry. His current focus is to identify and drive digital transformation opportunities within the civil engineering industry. At SoftTech, he heads product strategy for construction and asset operations solutions. Prior to SoftTech, Kashyap has rich experience of helping clients conceptualize and execute projects that spread across diverse sectors such as transportation, industrial, environmental, and water.
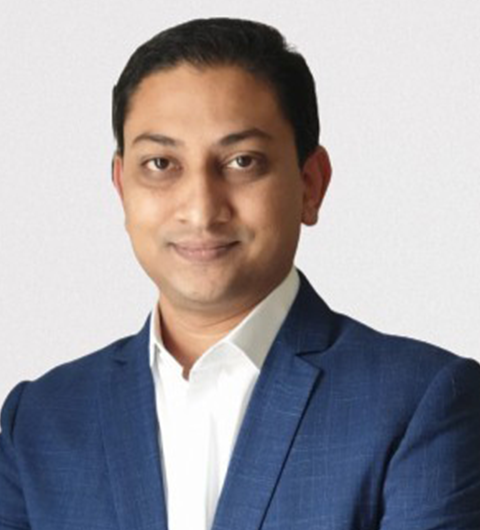
Construction, Metals and Mining Subvertical, Tech Mahindra
Sumit is a veteran professional with 17+ years of diverse experience in oil and gas, metals, mining, chemicals, petrochemicals, and construction domains. He excels in articulating execution digital strategies, collaborating with stakeholders on tactical and strategic initiatives, and developing digital transformational roadmaps. At TechM, he heads construction, metals and mining practice across globe, responsible for vertical P&L with focus on providing CxO advisory services.